How Smart Factories Integrate PLCs, Automation and Robotics
As we embark on the journey through the Fourth Industrial Revolution, the manufacturing sector continues to witness the seamless integration of PLCs (Programmable Logic Controllers), automation, and robotics, giving rise to the era of smart factories. Despite PLCs being developed almost six decades ago, their adaptability and efficiency persist alongside cutting-edge technologies. Let's delve deeper into this harmonious relationship and explore how manufacturers leverage these components to create the smart factories of tomorrow.
Smart Factories & PLCs: The Foundation of Process Automation
PLCs, the industrial computers that enable process automation, may not be household names, but their impact is unmistakable. PLCs convert inputs into outputs, translating signals from factory devices into actions. From stopping conveyors to saving power when no product is on the line to precisely timing product merges on assembly lines, PLCs execute commands that keep factories running like clockwork. Their origin precedes astronauts landing on the moon, yet today, they effortlessly coexist with cutting-edge manufacturing technology and robotics, proving their versatility and longevity. Initially designed to replace cumbersome hardwired relay logic systems, PLCs offered a simpler, more efficient alternative, propelling them into widespread use across all industrial environments. Their relevance remains to be investigated in the Industry 4.0 landscape, as emerging applications focus on data collection for analysis, aiding process improvement, and identifying efficiencies. Investing in PLC training is undoubtedly a smart move for those in the manufacturing sector seeking to future-proof their roles amid automation.
Automation in Smart Factories: Embracing Efficiency and Growth
While automation has sometimes been viewed as a threat to traditional manufacturing jobs, this concern is largely unwarranted. Instead, automation brings a wealth of opportunities and efficiencies to the factory floor that is truly fascinating. Manufacturers can minimize inefficiencies that hinder growth and profitability by replacing human-operator decision-making and manual responses with mechanized equipment and PLCs. This change enables skilled workers to concentrate on crucial and fulfilling activities, like developing programming logic for autonomous equipment or maintaining the equipment that carries out these tasks. Welding, assembly, lifting, cutting, and other repetitive tasks can now be expertly executed by robotic companions, freeing human workers to explore their full potential. Online technical training or industrial courses can empower laborers to navigate this transformation, ensuring a secure and promising future in the rapidly evolving industrial sector.
Smart Factory Robotics: The Synergy of Automation and AI
Often used interchangeably, robotics is, in fact, a subset of automation. Industrial robots, born from the post-World War II industrial boom, have proven invaluable assets in mass-producing consumer and industrial goods. By combining mechanical movement with advanced computer software, these robots operate with unparalleled speed and accuracy, outperforming even the most skilled human workers. As robotics advanced, "artificial intelligence" integration brought even more potential, enabling robots to simulate human reasoning, learning, and adaptability in their tasks. Far from replacing humans, robots collaborate harmoniously with workers, handling repetitive physical tasks and ensuring safety on the factory floor. While some robots remain stationary, others move autonomously, like the picking robots in distribution centers, seamlessly navigating their environments thanks to cutting-edge sensor technologies.
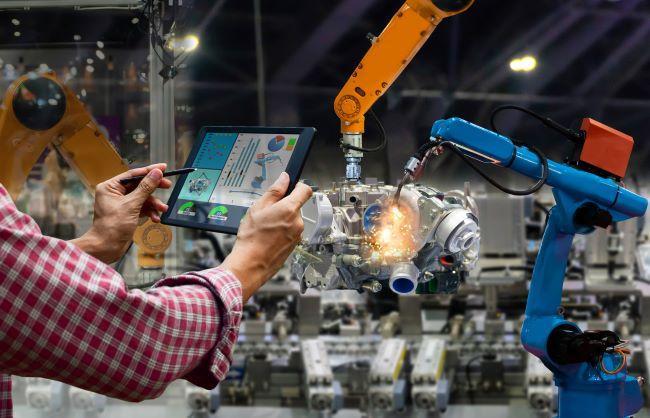
Benefits of PLC-Controlled Robots: Enhancing Efficiency and Versatility
According to research by Plan Engineering in 2021, companies gain a unified control point between industrial robots and programmable logic controllers with the development of PLC-controlled robots. Leveraging existing PLC programming expertise, manufacturers can streamline the integration and maintenance of new robotic equipment. It eliminates the need for specialized robot manufacturer experience, making managing the automated automation solution more efficient. As a single programming language often supports the entire solution, adopting PLC robot control simplifies troubleshooting and maintenance, leading to a quicker return on investment and reduced support costs. Manufacturers can also choose robot OEMs based on specific needs and capabilities, enhancing flexibility and efficiency in the factory environment. By reducing training costs and facilitating seamless upgrades, this approach ensures a faster return on investment and a more realistic path to integrating advanced robotic automation solutions.
The smart factories of the future will thrive on the integration of PLCs, automation, and robotics. As Industry 4.0 continues to unfold, embracing these transformative technologies will fuel growth and productivity and create new opportunities for skilled workers in the manufacturing sector.
To explore a wide array of online technical training programs, industrial courses, PLC training, or robotics training, discover what George Brown College offers. Empower yourself for the exciting future ahead in the world of smart factories.
If you’d like to learn more about PLCs and how to program them, consider checking out the PLC Technician Program or Robotics Technician Training Program at George Brown College.