Variable Frequency Drives: Basics and Common Applications of VFDs
Electric motors are used in multiple applications of our everyday lives but require the right amount of electrical energy to provide optimal torque and speed. To control these motors, Variable Frequency Devices (VFD), are used to convert AC current into DC current from the power supply. In this article we will look at how these devices work, and how they are important
History of VFDs
Nikola Tesla patented the first three-phase AC motor in 1887, which provided better efficiency and durability than Thomas Edison’s DC motor. However, controlling AC motor speed was difficult which resulted in the dependability of DC motors. It wasn’t after many decades that small components were designed giving rise to then current VFDs. The VFDs back then were used for heavy industry use, but as technology progressed, became more applicable to everyday use. Thanks to control hardware and the rise of microprocessors, VFDs have great versatility and provide less strain in the motor.
VFD components and function
VFDs are made up of 5 main components : Converter, DC link, Inverter, the Control Logic, and the User interface.
Converter
The converter, or AC input rectifier, help convert the AC voltage to a DC voltage. The converter is made up of multiple diodes that are connected parallel to each other and only allow the current to travel in one direction. The electricity that is flowing through the converter is cycled through until it is transformed into a rough DC voltage.
DC Link
DC Link is a filtering section made up of filter inductors and capacitors. The purpose of DC Link is to smoothen the rippled DC voltage obtained out of the rectifier circuit in the previous step. The filtered output is then fed to the input of the inverter.
Inverter
The purpose of the Inverter is to convert the output of the DC link, which is the filtered DC voltage, back into AC. The Inverter is used to control the variable voltage, variable frequency output to the motor. The Inverter is composed of IGBT switches that are connected in pairs to control the electrical flow. This is usually connected to a logic controller that allows an operator to interface and adjust the voltage of the motor. By controlling the path of electric flow with pulse-width modulation, AC voltage can be produced from the DC source.
User interface
To achieve optimal power usage or save energy, a user interface is needed to configure the VFD. A User interface is a control panel that is connected the VFD, allowing for manual user input. These range from a keypad to LCD touch screens. Newer systems offer Bluetooth wireless control panels.
Control logic
The user defined setting is then interpreted by the Control logic. It is the software needed for the VFD to communicate with the user interface and the feedback device on the motor. The software is usually based on a state diagram, which follows a set of sequences before completing a task from start to stop. This allows the VFD to be fully automated.
Why are VFDs important and how are they beneficial?
VFDs are basically a refinery that changes the rough AC voltage into a more stable current. By converting it to DC, it can be refined even further before being sent back out as an AC. This voltage that is sent out is square in shape rather than the traditional sinusoidal form, allowing for a gradual export of current. Some other benefits of VFDs include:
- Reduced energy consumption
- User-friendliness
- High power output
- Torque and speed control
- No soft starter for motor required.
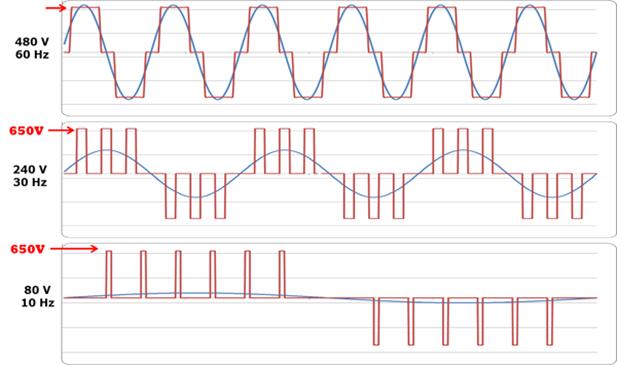
Applications of VFDs
VFDs have a wide variety of uses in electrical and motor-controlled systems. These systems require power regulating to conserve power when it isn’t required.
- Swimming pool filtration systems
VFDs can be used in indoor swimming pool filtration systems to increase cleanliness. VFDs used in indoor swimming pool filtration systems can help to lower the electricity consumption by easily varying the water volume as required. 40% of the power used by swimming pools is needed to filter the water. A pump using a VFD can aid in the recycling of water by drawing it into the filtration system.
- Pressure booster pumps
Commercial or large buildings like hotels require sufficient high water pressure to reach all units, including bathrooms and showers, using a pressure booster pump. VFDs can be a better alternative to pressure control valves since they have better energy savings and eliminates maintenance costs.
- HVAC systems
VFDs have been used in HVAC systems for decades. Traditionally they have been used for capacity modulation, but in recent years they have also been used for fan and pump balancing, equipment monitoring, and cutting equipment energy usage at peak load conditions. VFDs can help reduce the wearing of components of HVAC systems, as they require less energy to start a motor, thus reducing the components stress.
VFDs and PLCs
VFDs require an interface that allows a user to set the motor speed. PLCs or even DCS systems can be used to remotely control a VFD by automatically setting a drive speed for the motor to run at. PLCs can also be connected to a human machine interface, HMI, that allows the operator to set the motor speed manually. This allows for consistent voltage output when more electricity is needed.
As VFDs have become frequently used and reliable in the HVAC and electrical industry, electricians and PLC technicians benefit knowing and understanding how VFDs function and their applications.
To learn more about our PLC program please contact us! Speak with a Program Consultant, toll-free, at 1-888-553-5333 or email us at [email protected].
Comments
For more information…
Submitted by iris on Fri, 12/06/2024 - 08:21
For more information regarding our PLC program visit https://www.plctechnician.com/plc-ii-program-outline or contact a Program Consulant, toll-free at 1-888-553-5333.
Variable frequency drives basic and its common application
Submitted by Devanshu (not verified) on Thu, 12/12/2024 - 01:32
Great Post!
Will like to no more about variable frequency drive and its application. I would like to incorporate it in my solar power design to operate LNG ( gas ) and PMS / diesel filling stations that have many pumps in operation.